Comprehensive Overview: What is Porosity in Welding and Just How to stop It
Comprehensive Overview: What is Porosity in Welding and Just How to stop It
Blog Article
Porosity in Welding: Identifying Common Issues and Implementing Ideal Practices for Avoidance
Porosity in welding is a pervasive concern that frequently goes unnoticed until it creates significant troubles with the integrity of welds. In this conversation, we will certainly check out the vital elements adding to porosity formation, analyze its detrimental results on weld performance, and go over the best methods that can be taken on to minimize porosity incident in welding procedures.
Common Sources Of Porosity
Utilizing dirty or wet filler materials can present pollutants into the weld, adding to porosity problems. To reduce these usual reasons of porosity, detailed cleaning of base metals, correct protecting gas option, and adherence to ideal welding specifications are vital practices in accomplishing premium, porosity-free welds.
Effect of Porosity on Weld High Quality

The presence of porosity in welding can dramatically jeopardize the structural stability and mechanical residential properties of welded joints. Porosity develops voids within the weld metal, deteriorating its general strength and load-bearing capacity. These spaces act as anxiety concentration points, making the weld extra vulnerable to fracturing and failure under applied tons. In addition, porosity can decrease the weld's resistance to deterioration and other ecological aspects, additionally lessening its long life and performance.
Welds with high porosity levels have a tendency to display reduced influence toughness and lowered capability to warp plastically before fracturing. Porosity can hinder the weld's ability to effectively send forces, leading to premature weld failure and prospective safety hazards in crucial structures.
Finest Practices for Porosity Prevention
To enhance the structural honesty and quality of welded joints, what certain actions can be implemented to reduce the incident of porosity throughout the welding procedure? Using the correct welding method for the certain product being bonded, such as readjusting the welding angle and gun position, can even more stop porosity. Normal inspection of welds and immediate remediation of any look at more info problems identified throughout the welding procedure are vital techniques to prevent porosity and produce top quality welds.
Significance of Appropriate Welding Methods
Applying appropriate welding strategies is extremely important in making sure the structural integrity Recommended Site and top quality of welded joints, constructing upon the foundation of effective porosity avoidance measures. Too much heat can lead to raised porosity due to the entrapment of gases in the weld pool. In addition, utilizing the ideal welding specifications, such as voltage, present, and take a trip speed, is crucial for accomplishing audio welds with very little porosity.
In addition, the option of welding procedure, whether it be MIG, TIG, or stick welding, should line up with the specific demands of the task to guarantee optimum results. Correct cleaning and prep work of the base steel, as well as choosing the appropriate filler material, are likewise essential elements of skillful welding techniques. By sticking to these ideal practices, welders can minimize the danger of porosity development and create high-grade, structurally sound welds.
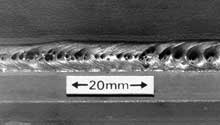
Checking and Top Quality Control Steps
Evaluating procedures are vital to discover and stop porosity in welding, making sure the toughness and longevity of the last item. Non-destructive screening techniques such as ultrasonic testing, radiographic testing, and visual inspection are commonly employed to recognize possible flaws like porosity.
Carrying out pre-weld and post-weld evaluations is also essential in keeping quality assurance standards. Pre-weld inspections entail verifying the products, devices settings, and sanitation of the work location to avoid contamination. Post-weld inspections, on the other hand, analyze the last weld for any type of issues, consisting of porosity, and verify that it meets specified standards. Carrying out an extensive top quality control plan that consists of extensive testing treatments and inspections is vital to lowering porosity problems and making certain the general top quality of welded joints.
Final Thought
To conclude, porosity in welding can be an usual issue that affects the top read more quality of welds. By recognizing the common causes of porosity and carrying out ideal techniques for avoidance, such as proper welding techniques and testing steps, welders can make sure excellent quality and trustworthy welds. It is vital to focus on prevention techniques to decrease the event of porosity and keep the integrity of bonded frameworks.
Report this page